Oil & Gas Sector
The oil and gas industry involves complex processes and the handling of hazardous substances in high-temperature, high-pressure environments. Ensuring safety for personnel and the environment is critical. Non-destructive Testing (NDT) plays a vital role in maintaining the integrity and safe operation of processing plants, storage facilities, and transport equipment across the oil and gas industry.
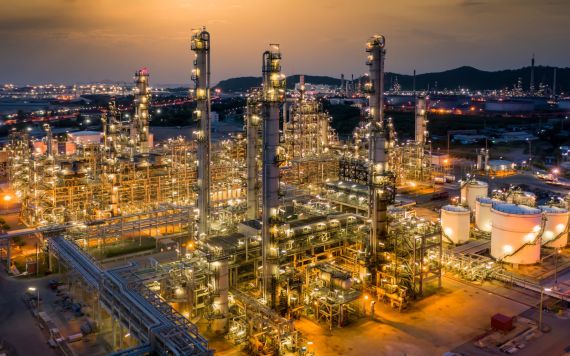
Ultrasonic Testing (UT) in Oil and Gas
Ultrasonic (UT) inspection methods are widely used in the oil and gas sector. These techniques are essential for weld inspections and corrosion assessments, enabling plant engineers to evaluate equipment integrity, identify defects, and address conditions that might result in equipment failure or loss of containment. This approach supports the industry’s commitment to maintaining high-quality standards and ensuring operational safety.
1. Inspection Goals
- Weld Inspection: Detecting manufacturing or in-service discontinuities such as cracking, lack of fusion, porosity, or inclusions.
- Corrosion Survey: Measuring wall losses in piping or vessel shells caused by corrosion or erosion.
- Hydrogen attack Survey: Finding hydrogen inclusions, delamination and cracks caused by the progress of hydrogen contamination. This degradation mechanism occurs when the asset is subject to high pressure and high temperature cycles.
2. Challenges
- Access Constraints: Plant items are often insulated with lagging that must be removed before inspection. Chemical plants are large and may require scaffolding, rope access, or MEWPs to reach equipment.
- High Temperatures: Inspections may involve equipment operating at high temperatures, necessitating specialised tools and techniques.
- Complex Geometries: Pipework often includes multiple bends and tees, creating intricate inspection challenges.
Specialised NDT Solutions for the Oil and Gas Industry
Sonatest offers advanced solutions tailored to the needs of the oil and gas sector. The VEO3 is a multi-technique system designed for phased array weld inspection, corrosion mapping, and advanced methods such as Total Focusing Method (TFM), TFMiTM, and Time of Flight Diffraction (TOFD). These capabilities address a wide range of challenges in non-destructive testing for oil and gas.
The WheelProbe 2 is ideal for rapid corrosion mapping over large areas, using minimal water and enhancing efficiency.
The Wave interactive flaw detector, with its CAD import scan plan, visualises complex geometries, allowing inspectors to pinpoint the origin of signals. This feature helps distinguish between geometric signals and defect indications, reducing false calls, saving time, and cutting costs.
NDT in Oil and Gas: Ensuring Quality and Safety
Non-destructive testing in the oil and gas industry is essential for quality assurance and operational reliability. Whether addressing weld integrity or corrosion issues, NDT ensures the continued safety and efficiency of operations in this critical sector. Using the NDT data, it is possible to predict the end-of-life of expensive assets. An exhaustive monitoring provides reliable inputs to the integrity models. Using NDT in maintenance helps that industry to reach cost effective, quality and safety goals.
Frequently Asked Questions
Ultrasonic testing (UT) primarily serves to inspect welds and assess corrosion across oil and gas infrastructure. It helps engineers evaluate the structural integrity of pipelines, vessels, and other critical equipment, identifying defects that could lead to failures or environmental hazards.
At Sonatest, our VEO3 is a versatile non-destructive testing system capable of multiple advanced techniques such as phased array weld inspection, corrosion mapping, TFM, and TOFD. This multi-technique capacity allows for detailed and efficient assessments of equipment integrity, crucial in maintaining safety standards in the oil and gas sector.
Inspectors often deal with challenges such as limited access to inspection sites, which may require the removal of protective insulation or the use of scaffolding and rope access. High operating temperatures and complex pipework geometries further complicate the inspection process, demanding specialised equipment and techniques.
At Sonatest, the Wave detector enhances flaw detection using its CAD import scan plan, which provides a visual map of complex geometries. This helps inspectors distinguish between geometric and defect signals accurately, reducing false positives and improving the efficiency of the inspection process. This capability is particularly valuable in the oil and gas industry when the weld region of interest is difficult to evaluate.
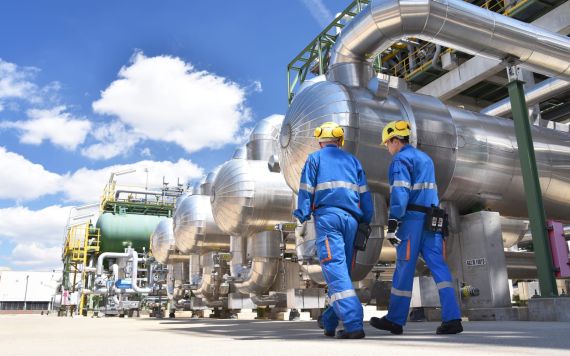