Aerospace Astronautical Inspection
The aerospace industry encompasses a dynamic and technologically advanced industry, this is most plain in the Astronautical sector where technological advances in materials and structures is on the cutting edge.
With technology constantly advancing in new materials and designs, it has never been more important to have a culture of safety and quality, this includes the inspection of satellite parts, engine structures, launch pad systems and much more.
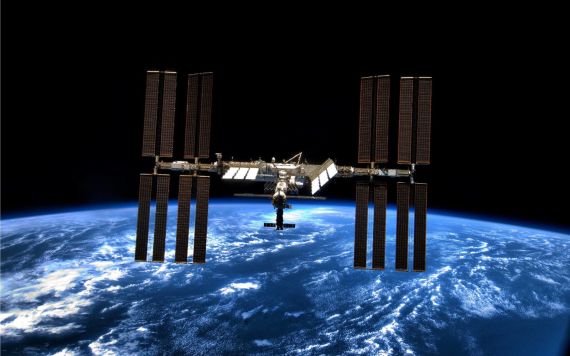
Inspection is crucial role in ensuring the safety and reliability of astronautical equipment. Some of the parts and materials used will be destined for permanent service in space, be that in Earth orbit or out into the solar system, the only chance for inspection is prior to launch, this put added pressure on the inspection to be highly accurate first time for these mission critical parts. Some of the challenges and goals of inspection are:
1. Inspection Goals
- Structural Integrity Verification: Ultrasonic inspection helps verify the structural integrity of components. It detects internal defects such as voids, delamination’s, and disbond that may compromise the part’s strength.
- Quality Assurance and Safety: By finding defects early in the manufacturing process or during service, ultrasonic inspection helps ensure only high-quality parts are used, and detecting hidden flaws prevents catastrophic failures during flight, enhancing passenger safety.
- Adherence to Regulatory Compliance: Airworthiness regulations mandate thorough inspections to meet safety standards.
2. Challenges
- Complex Geometry: Astronautical components often have intricate shapes, making it challenging to achieve complete coverage during inspection.
- Composite Materials: Composite structures pose unique difficulties due to their layered nature. Ultrasonic waves may scatter or attenuate differently in composites compared to metals.
- Surface Conditions: Surface roughness, curvature, and coatings impact ultrasonic wave coupling and signal quality.
- Access Constraints: Some areas are difficult to access (e.g., internal cavities), forcing the inspector to use a short, low-profile, flexible array or even custom probes.
- Large Surfaces: Ensuring complete coverage on large composite surfaces requires efficient scanning techniques.
- Real-Time Detection: Immediate detection of damage during flight tests is desirable but it requires a solid integration to combine NDT (Non-Destructive Testing) instruments, PCs and mechanics.
Sonatest has specialised solutions for inspecting aerospace assets. The RSFlite, which is specifically designed for composite and large-area inspections, when paired with the Wheel Probe 2 scanner, allows large areas to be scanned quickly showing instant results and creating data packs that can be reviewed on UTMap, a software specifically designed for C-Scan data review.
For smaller detail areas our range of phased array transducers and wedges can provide solutions for inspection coverage.
The Wave interactive flaw detector with its CAD import scan plan allows the visual representation of complex geometry parts, showing exactly where signals are originating from making it easier to differentiate a geometric signal from a defect signal, reducing false calls and saving time and money in the process.
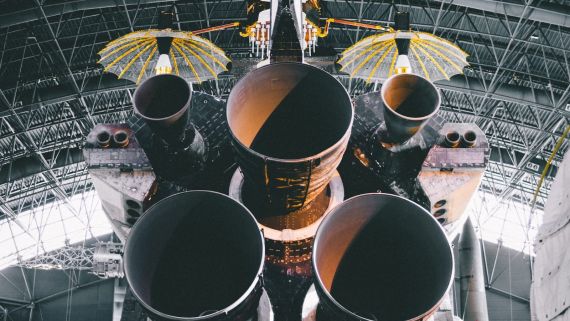