Mining Sector
Mining has played a crucial role throughout history, from ancient civilizations, through the Industrial Revolution with coal and into the modern era.
Although mining may seem to be an ageing practice, the demand for minerals for low-carbon technology, such as solar panels, batteries for electric vehicles, wind turbines, etc, means that mining is a massive industry vital for the future.
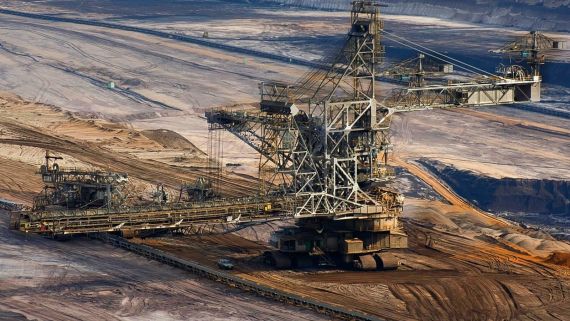
The demand for minerals has only increased with technological advances, rare earth minerals requiring specialist mining techniques to be developed and implemented in evermore demanding environments. Low-carbon technology, such as solar panels, batteries for electric vehicles, wind turbines, etc, means that mining is a massive industry vital for the future.
The Role of NDT in Mining
NDT (Non-Destructive Testing) in mining plays a crucial role in evaluating the integrity and proper functionality of equipment and structures that are working in incredibly harsh environments. An unplanned shutdown due to a failure of equipment can cause severe downtime and expense for repairs. When implemented correctly, NDT can highlight areas of potential failure before they happen, allowing for mine owners to plan shutdowns and maintenance in advance.
Key Inspection Areas
- Welds: UT weld inspection highlights hidden discontinuities caused by construction and in-service damage.
- Structural integrity: UT inspection can highlight structural integrity issues such as wall losses due to corrosion.
- Conveyor belt reinforcement: UT inspection can show damage to conveyor belt reinforcement wires and show the integrity of repairs.
- Gear inspection on rock drums: PA checking cracks appearing at the tooth’s root.
- Pipeline with rubber lining: Thickness gaging or PA survey to check if the inner rubber layer remains in place or damaged. The rubber protects the steel from its high corrosive content and its failure can break the pipeline faster than usual corrosion processes.
Common Challenges in Mining Inspections
Harsh environments: Equipment can be in extremely harsh environments, the Sonatest equipment can handle temperature extremes and high particulate areas.
Sonatest Solutions for Mining
Sonatest has specialised solutions for all aspects of inspection in the mining industry. The VEO3 is a multi-technique specialist system capable of performing phased array weld inspection and corrosion mapping. Also included are TFM (Total Focusing Method), TFMi and TOFD (Time of Flight Diffraction) inspection methods, each providing further inspection solutions to the inspector.
Advanced Tools for Efficient Testing
- The WheelProbe 2 allows large areas to be corrosion mapped quickly and with minimum water needed in the area.
- The Wave interactive flaw detector with its CAD import scan plan allows the visual representation of complex geometry parts, showing exactly where signals originate from. This makes it easier to differentiate a geometric signal from a defect signal, reducing false calls and saving time and money in the process.
- The Wave workflows are simple. You can achieve thickness measurements and send report data in the next minute. (A network with internet must be available in the inspection area)
Ensuring Quality and Safety
Sonatest solutions provide techniques to meet the requirements of the mining industry. Using advanced analysis and data from inspections, we help mining engineers detect potential issues and ensure safety and quality at mining sites. With proper information and inspection systems, Sonatest helps optimise operations and support engineering excellence.
Frequently Asked Questions
Ultrasonic testing (UT) plays a crucial role in ensuring the safety, efficiency, and reliability of mining equipment and structures. It is used to inspect critical components such as conveyor belts, pipes, and welds for cracks, corrosion, or other hidden flaws. This non-destructive technique helps prevent failures and enhances operational safety in challenging mining environments.
UT allows for the early detection of wear, corrosion, and structural defects in mining equipment, enabling proactive maintenance. By identifying potential issues before they escalate, ultrasonic testing reduces downtime, minimises repair costs, and extends the lifespan of equipment like loaders, drills, and haul trucks.
Underground mining environments are high-risk and require rigorous safety standards. Non-destructive testing methods, including ultrasonic testing, provide a safe way to assess the condition of structural supports, ventilation shafts, and machinery without causing any damage. This ensures continuous operation and enhances worker safety.
Sonatest systems are designed to perform accurately and reliably in harsh mining conditions. With advanced features like phased array technology, corrosion mapping, and the Total Focusing Method (TFM), these systems deliver precise and efficient inspections in all environment conditions. Their rugged design and user-friendly interface make them ideal for on-site applications in the mining sector.
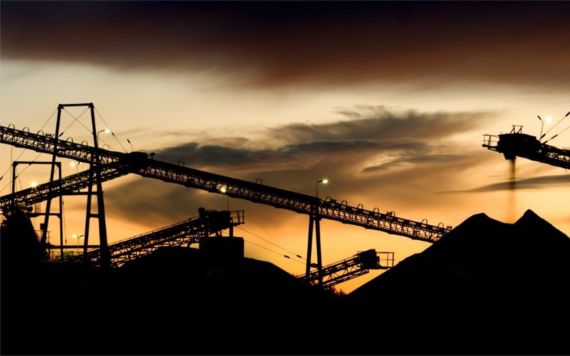