Chemical & Petrochemical
The chemical and petrochemical industries involve complex processes with hazardous substances in high-temperature high-pressure environments; the safety concerns to personnel and the environment are paramount. NDT (Non-Destructive Testing) inspection plays a pivotal role in the continuing safe operation of processing plants, storage facilities and transport equipment.
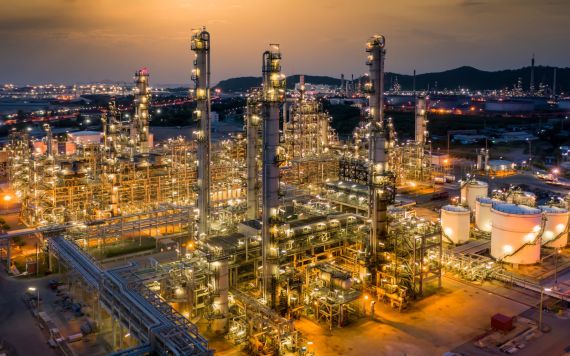
Ultrasonic (UT) inspection methods are used widely across the chemical and petrochemical industry; their primary uses are weld inspections and corrosion assessments to help plant engineers assess the integrity of their plant equipment, find defects or conditional that may lead to an equipment failure or loss of containment.
1. Inspection Goals
- Weld Inspection: Detection of manufactured or in-service discontinuities such as cracking, lack of fusion, porosity or inclusions.
- Corrosion Survey: Detection and measurement of wall losses in piping or vessel shells due to corrosion or erosion
2. Challenges
- Access Constraints: Plant items are often protected/insulated with lagging, this needs removing prior to inspection. Chemical plants are large systems where access is often only available via scaffolding or MEWPs.
- High Temperatures: The inspection target can be at high temperatures, requiring special equipment to perform the inspections.
- Complex Geometries: Pipework can often wind through the plant to get to its destination; this can cause multiple bends and tees, creating complex and restricted access inspection challenges.
Sonatest has specialised solutions for all aspects of inspection on chemical and petrochemical sites. The VEO3 is a multi-technique specialist system capable of performing phased array weld inspection and corrosion mapping, also included are TFM (Total Focusing Method), TFMi and TOFD (Time of Flight Diffraction) (Time of Flight Diffraction) inspection methods, each providing further inspection solutions to the inspector.
The Wheel Probe 2 allows large areas to be corrosion mapped quickly and with minimum water needed in the area.
The Wave interactive flaw detector with its CAD import scan plan allows the visual representation of complex geometry parts, showing exactly where signals are originating from making it easier to differentiate a geometric signal from a defect signal, reducing false calls and saving time and money in the process.
Frequently Asked Questions
Non-Destructive Testing (NDT) is critical in these industries to ensure the safety and functionality of facilities under high-pressure, high-temperature conditions. NDT methods like ultrasonic testing enable engineers to detect inconsistencies in welds and assess corrosion without harming the equipment. Providing accurate and precise evaluation through time is crucial for preventing potential failures and maintaining operational integrity.
Sonatest utilises ultrasonic flaw detectors like the WAVE and advanced technology such as the VEO3 multidisciplinary system and the Wheel Probe 2 for efficient and precise corrosion mapping. These instruments solve many inspection scenarios that require NDT attention. The instrument, scanner and probe can cover asset inspections for: pipelines, storage tanks of all kinds, nozzles, welds, flanges, etc.
Sonatest offers conventional ultrasonic technologies for weld and corrosion inspections and advanced ultrasonic methods like Total Focusing Method (TFM), Time of Flight Diffraction (TOFD), and phased array inspection capabilities. These technologies allow for high-resolution imaging and precise flaw detection, crucial for defect evaluation that require rigorous examination of materials and structures.
Sonatest's Veo3 is valued for its precision and adaptability in various inspection scenarios, including complex material assessments. They are engineered to deliver accurate results quickly for all ultrasound techniques, which is invaluable for maintaining high standards of safety and quality in critical operations.
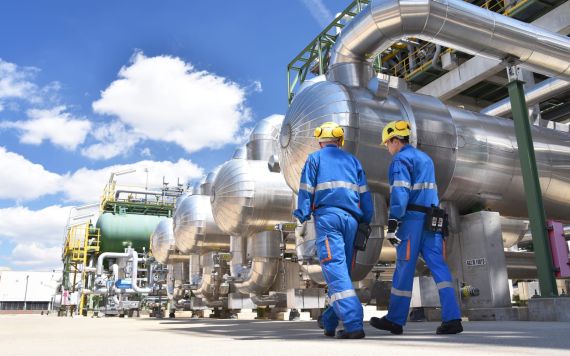