Thickness Gauges
An ultrasonic thickness gauge is particularly useful for non-destructive thickness measurement when access is only possible from one side of the material, for example pipes or tanks. Thickness measurement can be performed on most common engineering materials, such as metal, plastic and glass.
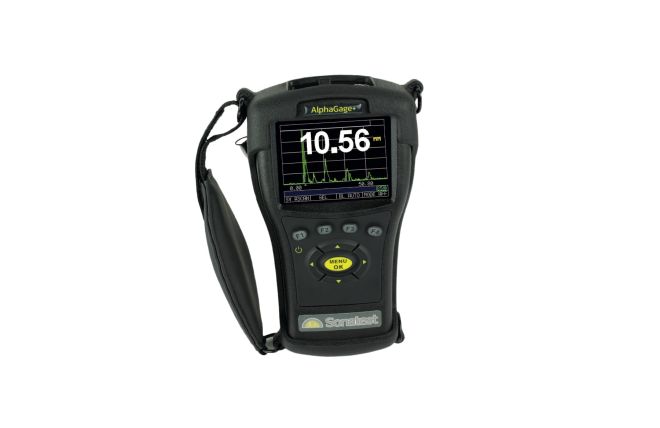
Non-destructive Thickness Gauging
An ultrasonic thickness gauge is a crucial instrument in non-destructive testing (NDT), operating on principles similar to sonar but at much higher frequencies. A transmitter emits a short pulse of ultrasound into the material. This pulse reflects off the opposite surface and returns to a receiver. By analyzing the time it takes for the pulse to return, the thickness gauge calculates and displays the material thickness. This method allows for precise thickness measurement without causing any damage, making it indispensable in various industrial applications.
Thickness Gauges FAQs
Many industries—such as building, construction, and manufacturing—have strict standards and regulations regarding the minimum allowable thickness of materials for specific applications. Ultrasonic thickness gauges are used to accurately measure and verify that material thicknesses meet these requirements, ensuring adequate protection and quality.
Regular thickness measurements are essential not only for inspecting new equipment fabrications but also for monitoring in-service items. Consistent measurement helps predict corrosion and erosion rates, enabling the assessment of remaining service life and proactive maintenance planning.
A thickness gauge measures thickness by emitting an ultrasonic pulse into the material and calculating the time it takes for the echo to return from the opposite surface. This time measurement, combined with the known speed of sound in the material, allows the gauge to determine the exact thickness.
Ultrasonic thickness measurement is highly accurate, often providing precision within a few hundredths of a millimetre. The accuracy depends on the quality of the equipment, the properties of the material being tested, and the expertise of the operator. Proper calibration and a suitable environment can enhance its accuracy, making it a reliable choice for critical measurements.
Ultrasonic thickness gauges offer several advantages:
- Non-destructive: They measure thickness without damaging the material, which is perfect for ongoing inspections
- Versatile: These gauges can be used on a wide range of materials, including metals, plastics, ceramics, and composites
- Efficient: Measurements can be taken quickly and from one side of the material, which is ideal for objects in difficult to access areas
- Safe: Ultrasonic gauges are safe to use as they do not emit harmful radiation, unlike some other non-destructive testing methods
Ultrasonic thickness testing is generally not suitable for materials that are highly porous or have coarse grain structures, such as certain types of wood or foam. These materials can scatter the ultrasonic waves, making it difficult to obtain accurate readings. Additionally, materials that lack parallel surfaces or are extremely thin might also present challenges for ultrasonic testing.