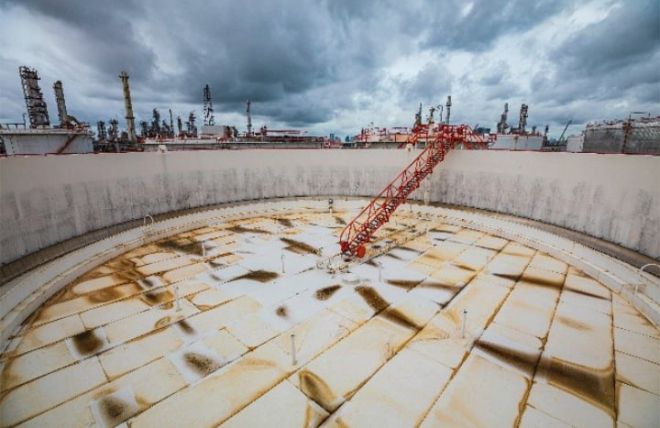
A ‘Floating pontoon’ roof on a storage tank is designed to sit directly onto the contained product and move higher or lower with that product as it is directed in and out of the tank.
They are generally deployed when storing volatile products like gasoline and can be used on their own or with a fixed-roof tank.
There are 3 main types of floating roof structures:
- Single-deck pontoon types
- Double-deck types
- Specialty design, buoy designs, radially reinforced roof structures etc.
There are certain key areas of inspection on floating roofs; in this blog, we will detail these specific areas; our previous blog on Fixed Roof Inspection covers the main inspection methods used on tank roofs; for further details, follow this link to the blog.
Pontoon Inspection
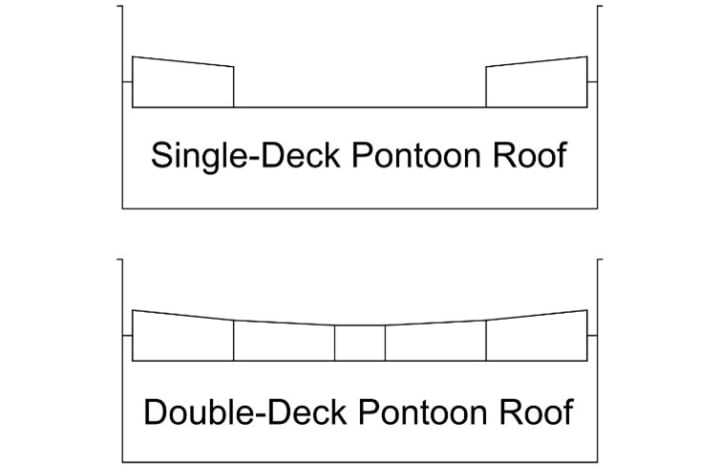
Both single and double-deck roofs rely on buoyancy provided by pontoon compartments. In single-deck roofs, this buoyancy is achieved through an outer radial ring, while double-deck roofs use concentric rings covering the entire surface. The primary concern is the potential failure of these pontoons, which could result in them taking on rainwater or the product itself, causing the roof to sink or tip. Such failures are typically due to weld defects or corrosion, leading to holes in the pontoons.
To mitigate these risks, pontoons are regularly inspected for signs of corrosion or leakage. Common inspection methods include ultrasonic thickness surveys and weld inspections, which help ensure the integrity of the pontoons.
For further information on our equipment and application notes, follow these links:
Ultrasonic Flaw Detectors, VEO3, Thickness Gauges
Landing Leg and Guides Inspection
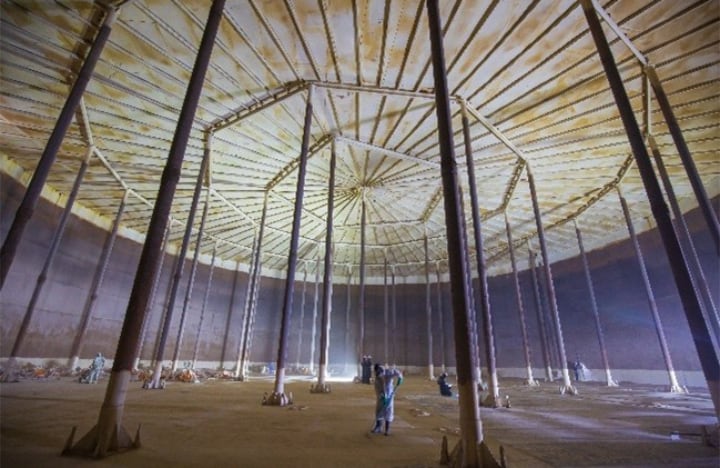
When lowering or emptying the tank, the floating roof will eventually ‘land’ or come to rest on an array of support legs. This allows a vapor space to form, and when empty, maintenance and inspection work can be carried out on the floor, lower shell, and underside of the roof.
Because the legs are critical for supporting the full weight of the roof and are only accessible during a complete maintenance shutdown, they are inspected for corrosion or any other defect that may cause a failure. This is primarily UT thickness inspection of the fixed landing point, the shaft of the leg, and the guide points located on the roof itself.
Using T-Log on Sonatest’s flaw detectors, large quantities of data can be recorded and transferred to an CSV file format for easy reporting.
For further information on our equipment and application notes, follow these links:
T-Log, Ultrasonic Flaw Detectors, 0° Ultrasonic Transducer Range
Floating Roof Drain Systems
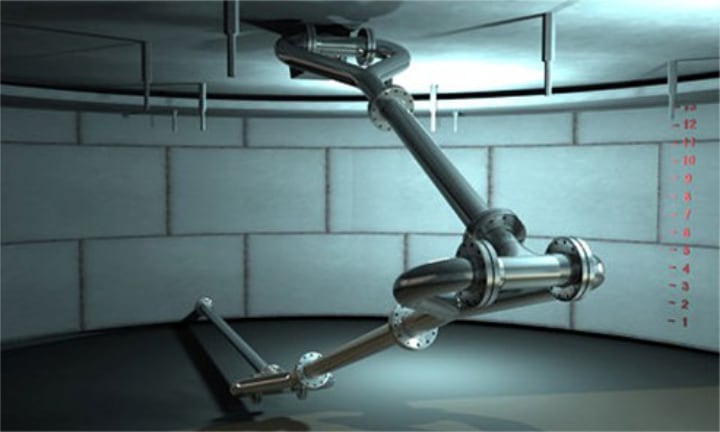
One of the primary dangers associated with floating roofs is flooding due to rain. To mitigate this risk, floating roofs are equipped with one or more drainage lines that channel water from the roof to a sump or outlet from the tank. These pipes are located beneath the roof and operate within the stored product.
The drainage pipes can be made of steel or reinforced flexible rubber, designed to articulate as the roof rises and falls. If these pipes fail, rainwater can contaminate the stored product, or the product can leak into the tank farm's outlet system. Articulated drain image courtesy of We-Couplings Ltd.
Ultrasonic inspection can be used to determine the remaining wall thickness of the drainage system, allowing for early detection of corrosion or erosion.
For further information on our equipment and application notes, follow these links:
T-Log, Ultrasonic Flaw Detectors, 0° Ultrasonic Transducer Range