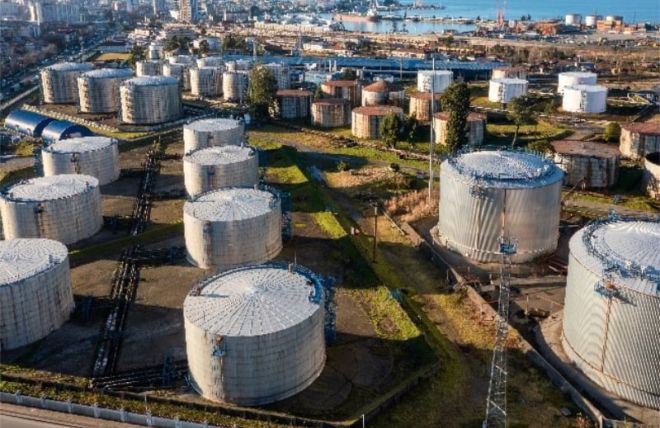
This blog is the first in a series in which we will explore the wide range of inspection requirements for above-ground cylindrical storage tanks, from routine checks to full shutdown, and external and internal assessments of all major components and ancillaries.
We will identify the many applications where Ultrasonic Testing (UT) is suitable and show how Sonatest’s leading UT technology can be used to increase productivity, provide high-quality repeatable data capture and streamline the inspection process to ensure your storage tanks remain serviceable and safe during operation.
Storage Tank Design and Inspection Codes Driving Safety Standard
Storage vessels are among the most critical safety assets in all industry sectors. They are responsible for containing thousands of tons of hazardous liquids and gases per tank. These substances can be toxic, flammable, corrosive, or pose a danger due to the sheer quantity stored.
Codes and Standards for Construction and Inspection
The construction and inspection codes for storage tanks vary worldwide. The primary design codes include API 620, API 650, and EN 14015. These standards regulate the design and construction of large, welded, low-pressure storage tanks, welded tanks for oil storage, and site-built, vertical, cylindrical, flat-bottomed, above-ground, welded steel tanks, respectively.
Inspection standards, such as API 653 and EEMUA 159, provide guidelines for the inspection, repair, alteration, and reconstruction of above-ground storage tanks. They offer comprehensive guidance on the inspection, maintenance, and repair of above-ground vertical cylindrical steel storage tanks.
Core Goals of Design and Inspection Codes
These codes aim to ensure the containment of pressure caused by product weight and vapour pressure, prevent leaks and catastrophic loss of containment, and detect defects early through regular inspections. They also emphasize the importance of implementing repair procedures that do not weaken the tank structure.
Long-Term Safety and Operational Efficiency
When correctly implemented, a thorough inspection regime can keep storage vessels safe and operational for decades. There are examples of tanks in operation today that are over 100 years old!
Storage Vessel Failure Mechanisms
When it comes to storage tank failures, corrosion is often the primary culprit. If we don't address it promptly, it can lead to holes and loss of containment. However, perhaps even more concerning is the overall weakening of the tank's structure caused by corrosion. For instance, areas where the metal has thinned can buckle under wind loading. This flexing can introduce extra stresses in the welds, which might lead to cracking. In extreme cases, the tank might not be able to handle the pressure of the stored product, resulting in a critical failure.
Other mechanisms are also at play. Poor tank settlement can induce structural problems, and floating roofs can fail, compromising the tank's integrity. Weld failures are another issue, often stemming from existing welding defects or corrosion-related problems. Microbial-induced corrosion is also a factor, as microbial activity can accelerate the corrosion process. Additionally, tanks can collapse under vacuum conditions. While these mechanisms might seem minor individually, they can collectively pose a significant risk to the tank's safety.
External factors shouldn't be overlooked either. For example, impacts from moving equipment like crane lifts or tanker movements can cause mechanical damage or even breach the vessel shell, leading to loss of containment.
Primary Inspection Areas
In storage tank inspections, there are certain areas where condition information is critical. Assessments of these areas are carried out at regular intervals, even if that is as simple as a visual inspection. Some of these checks can be carried out with the vessel ‘in service’ but others require the full shutdown, emptying and cleaning of the vessel. We explore these key areas below and will go into further detail in this blog series.
Roof (Floating, Fixed cone and Geodesic)
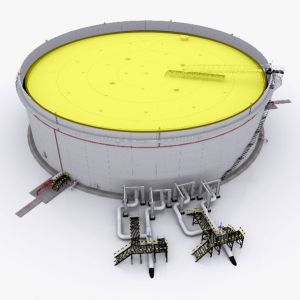
Above-ground storage tanks have several roof design options, which can be categorized into two types: fixed roofs and floating roofs. Each type serves specific purposes depending on the material being stored. In some cases, a tank may feature both a fixed roof and an internal floating roof.
The roof is a critical component of the tank, serving multiple functions. It acts as containment, supports safety-critical pressure valves, and houses measurement sensors and sampling points. Walkways and bridges between tanks are common features on the roof. All these elements require the roof and its ancillary parts to be in good working condition to ensure the proper functionality of the tank and the safety of personnel working on and around it.
This series will explore the ultrasonic inspection methods used on the roof, including thickness measurement, full corrosion mapping, nozzle weld inspection, and flange face inspection. These are all critical areas that demand a high level of accuracy and data analysis tools, which are provided by our equipment.
Shell
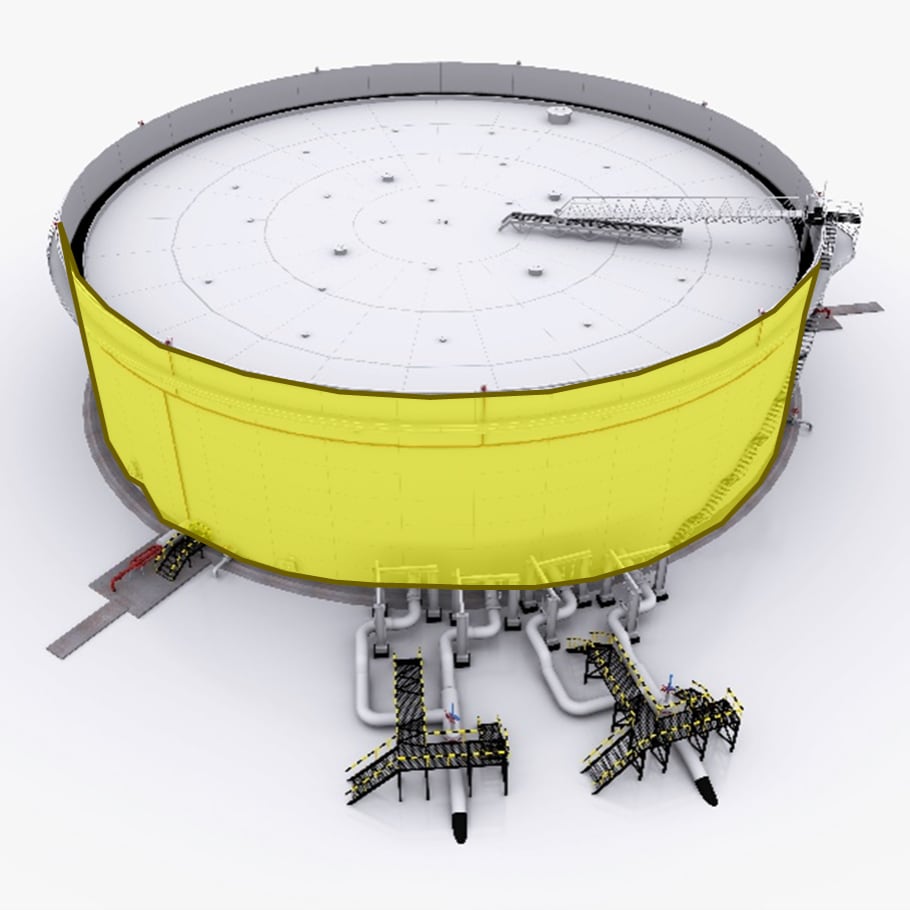
The primary function of the tank shell is to contain the pressure loading (hydrostatic head) of the liquid stored within the vessel. Design codes provide calculations for the thickness, material, welding type, requirements for wind girders, and more, depending on the type of liquid being contained, the environment in which the tank will be built, and the expected service life.
Due to the safety-critical nature of the shell, it is inspected regularly (weekly or monthly, depending on the tank content and condition). In some cases, a daily visual inspection of the tank is conducted to look for leaks, corrosion spots, bulges, and buckles, aiming to record any issues as early as possible.
Because the shell is accessible (unless cladding is present), it is relatively easy to inspect while the tank is in service. Thickness surveys and full corrosion mapping surveys provide information about the internal condition of the tank shell without needing to empty the tank and perform a confined space entry. However, these methods do not offer 100% coverage of the shell, so periodic shutdowns and entries are still necessary to obtain a complete view of the internal condition of the shell.
This series will explore the manual and automated ultrasonic inspection methods available to inspectors, providing a comprehensive survey package for inspecting shell plates and welds.
Floor
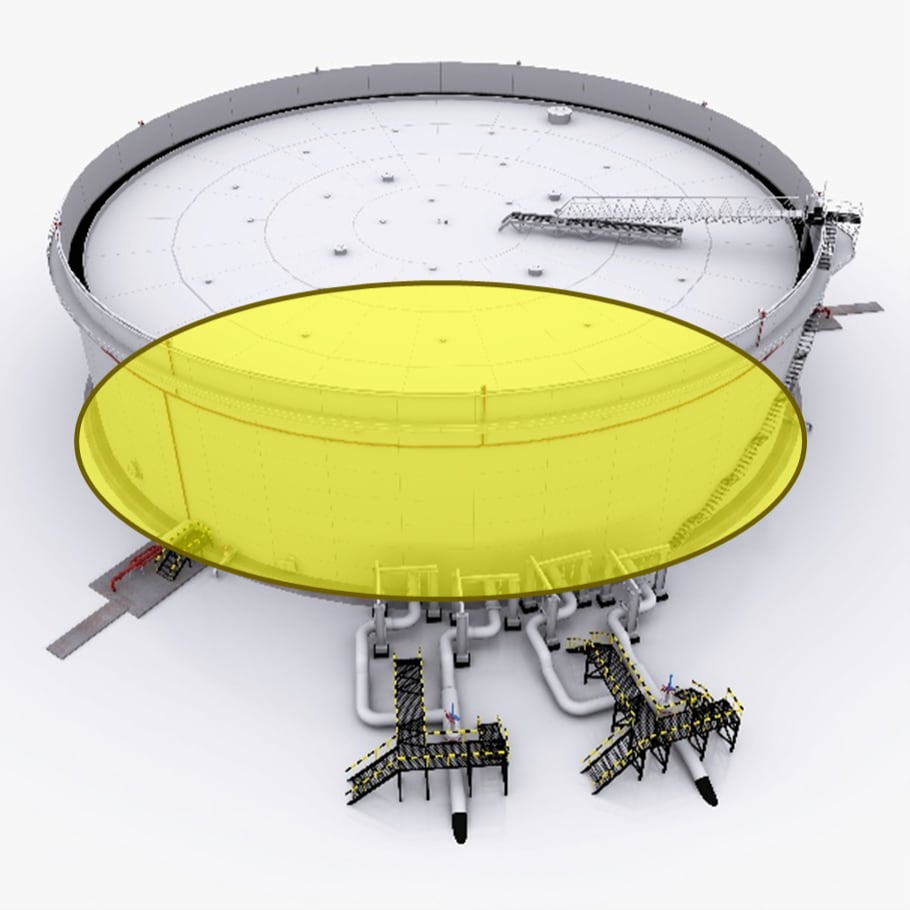
The floor of any tank is often considered the most critical area for inspection and faces a disproportionately higher inspection regime than other areas of the vessel.
This is largely due to the limited access available to the floor for inspection; it is only accessible when the tank is empty and clean. Coupled with the annular weld (the link between the shell and floor) being one of the most critical welds on the tank, when the opportunity arises, the floor undergoes a 100% inspection using multiple techniques to check for leaks, cracks, settlement issues, voids, and corrosion from both the topside and underside of the floor.
Ultrasonic methods can be utilized to thoroughly map the floor thickness in smaller tanks or in larger diameter tanks, covering inaccessible areas and providing highly detailed information on areas of interest identified through magnetic flux leakage scans, as well as inspecting the floor welds and sump areas, etc.
This series will explore how UT inspections can be utilized to quickly gather extensive data for use by the tank assessor in calculating the remaining life of the tank floor.
Pipework and Ancillary Equipment
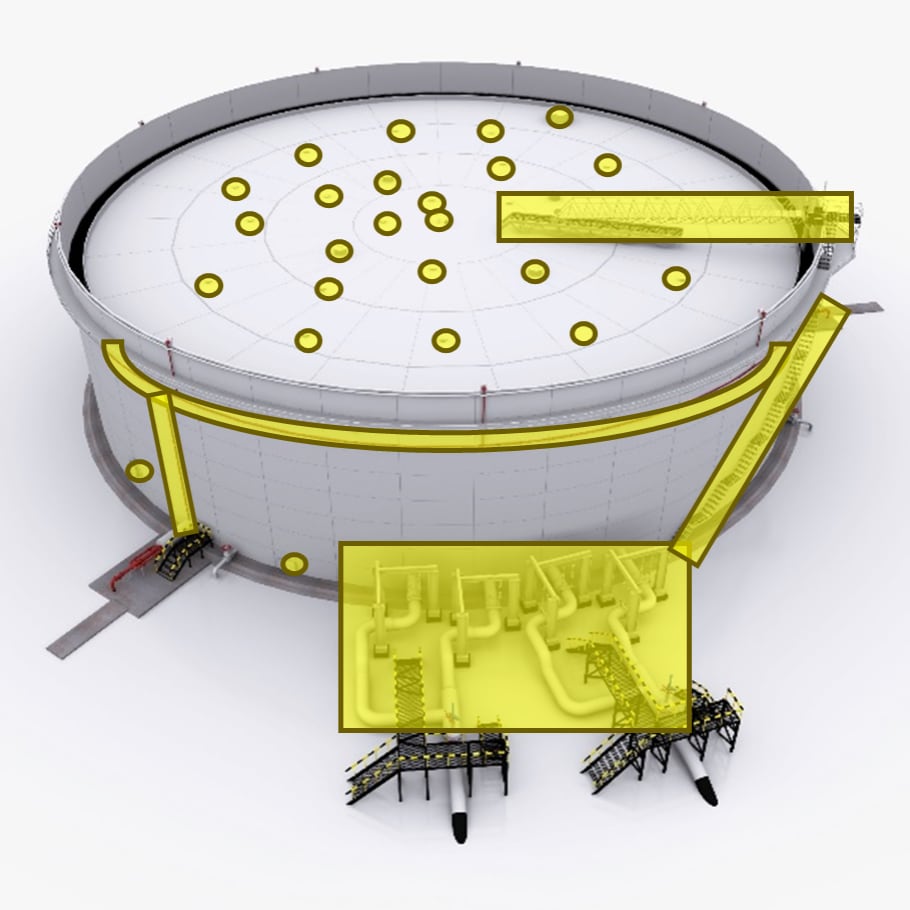
Pipelines are essential to a storage tank's functionality, facilitating the movement of product into and out of the tank. Nozzles on the tank shell and roof provide access to the tank as manways and connect to safety-critical pressure valves, level indicators, fire suppression systems, and more.
In this series, we will address the specific challenges associated with pipework on storage tanks. For an in-depth look at ultrasonic inspection of pipework, please refer to our previous blog series Pipeline Integrity 101 and our other Pipeline Integrity posts.
Storage tanks have numerous attachments, sensors, valves, and safety systems. These components provide operators with control and up-to-date information on product levels, temperature, and pressure, enabling them to manage an entire tank farm effectively. These attachments connect to the tank via nozzles, welding, and supports, and are accessed by stairs, ladders, and walkways. All these elements require regular assessment to ensure they are safe for personnel to operate and walk on.
Conclusion
Storage tank inspection requires qualified, highly skilled and experienced technicians to carry out the full range of methods required to cover all aspects of the tank structure and systems, and They must compile this data into a comprehensive report outlining the tank's overall condition, any necessary repairs, and potential adjustments to the operational limitations due to structural weaknesses.
At Sonatest, we supply equipment that is simple to use and produce in-depth ultrasonic data analysis tools to help inspectors easily incorporate the ultrasonic inspection scope of results into the final evaluation for the remaining life calculations for the tank.
In this blog series, we hope to provide you with beneficial information on where ultrasonic methods are used in tank inspection and how Sonatest’s systems and software can help technicians inspect with confidence.
Please contact our Applications Team if you have any questions. You can also find more solutions on our website.
To follow further content and our newsletter, please contact us and check “Add to mailing list”.