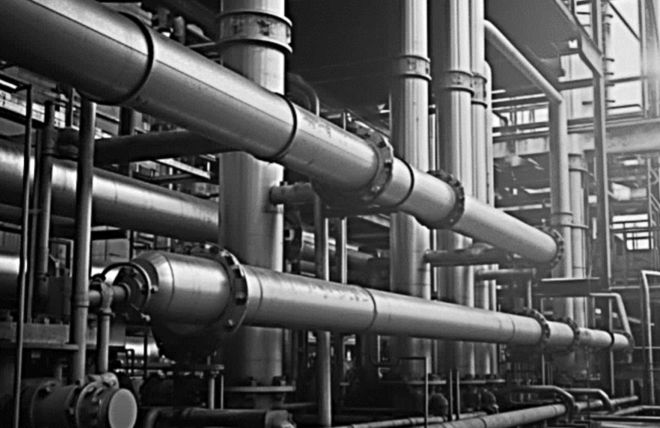
This blog is the first article regarding a broad pipeline integrity campaign. We will start with an overview of pipeline inspections. We will then develop more specific ultrasound content (blogs, solution notes, etc.) that is always related to pipeline assets. The goal is to provide NDT insights throughout this educational journey.
Pipeline Codes Driving its Integrity
The life cycle of pipelines should be monitored because they require critical quality control analysis. For example, there are pressure hazard factors to deal with, its intrinsic money asset value, the potential environmental accident consequences, and more to consider. Many standards regulate pipe structures to avoid disasters and hazards. The most known codes provide all the necessary requirements to achieve viable quality control. Among them are API, ASME, ASTM, and ISO.
- ASTM E213 – 22: Standard Practice for Ultrasonic Testing of Metal Pipe and Tubing
- ASTM E1961 – 21: Standard Practice for Mechanized Ultrasonic Testing of Girth Welds Using Zonal Discrimination with Focused Search Units
- API STD-1104 Welding of Pipeline and Related Facilities
- ISO 17635 – Non-destructive testing of welds – General rules for metallic materials
- ISO 5817 – Fusion-welded joints in steel, nickel, titanium and their alloys (beam welding excluded) - Quality levels for imperfections
There are also existing codes that cover distinctive cases, such as plastic pipe butt joints and austenitic steel lines and welds, high-pressure lines made of hardened steel, etc. Since you are now aware of the common regulations, let us check out the main non-destructive scenarios that can be applied to pipelines.
General NDT Methods for Pipeline Inspection
The next section contains two scenarios for inspection from the outside diameter surface (OD) and inspection from the inside diameter surface (ID). These locations get different inspection techniques separately because the defect characterization requirement may differ from time to time. For example, a full phased array mapping would not get the same remaining wall thickness data density and precision as a pulse eddy current mapping, even if both serve an adequate NDT evaluation approach.
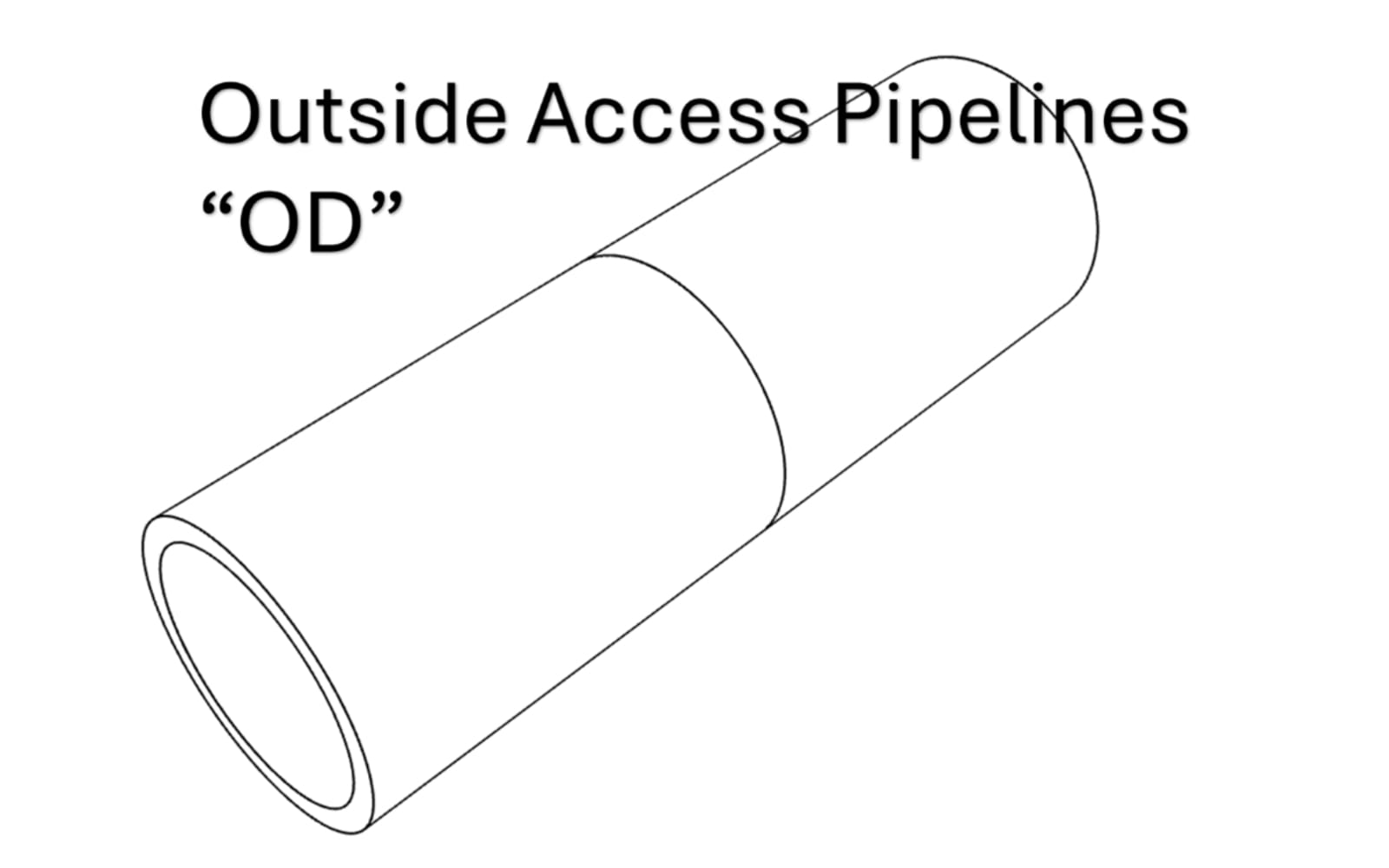
Techniques:
- Phased Array Ultrasound & Single Point UT
- Planned inspections or Constant Monitoring Systems
- Magnetic Flux Leakage
- Guided Wave (Sometimes known as Long Range UT)
- Magnetic Induced UT (EMAT)
- Acoustic Emission
Extra Challenges
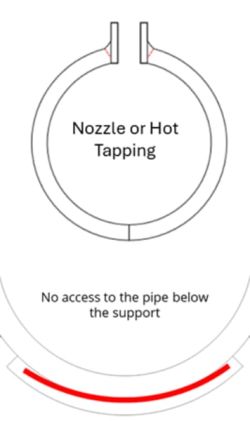
Limited access and complex geometries:
- Flanges (bolt-in survey with limited access)
- Elbows (especially mitered elbows)
- Valves
- Reducers
- Dissimilar materials/layered pipes
- Etc.
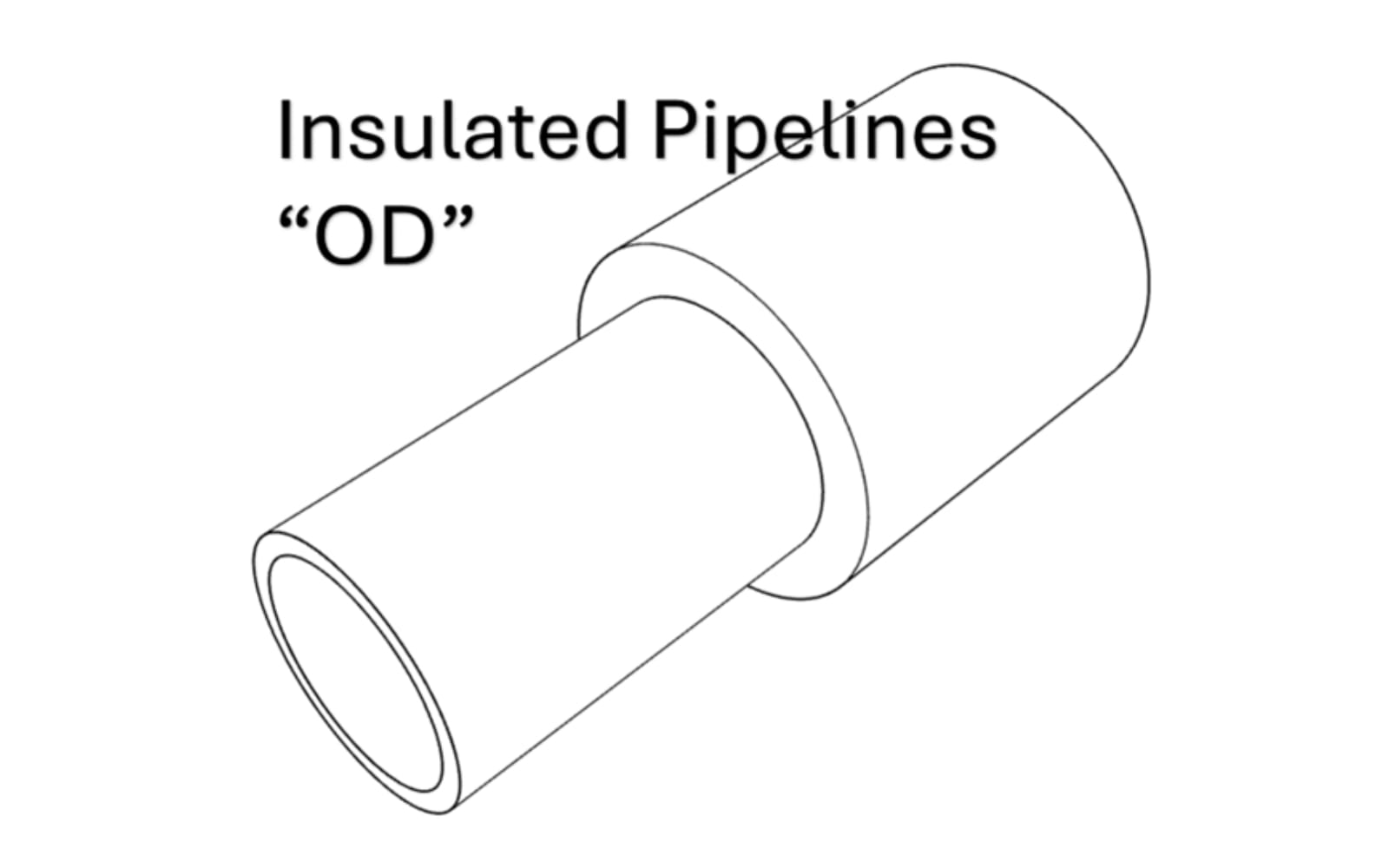
Techniques:
- Pulsed Eddy Current Array
- Guided Wave (AKA LRUT)
- Radiography
- Permanent Monitoring Systems
- Acoustic Emission
Extra Challenges
- Insulation is not ultrasound compatible
- Buried pipelines
- Pipe configuration is sometimes unknown
- Small diameter pipeline configuration may not allow all ID crawlers
- Lower precision techniques may require further NDT assessments
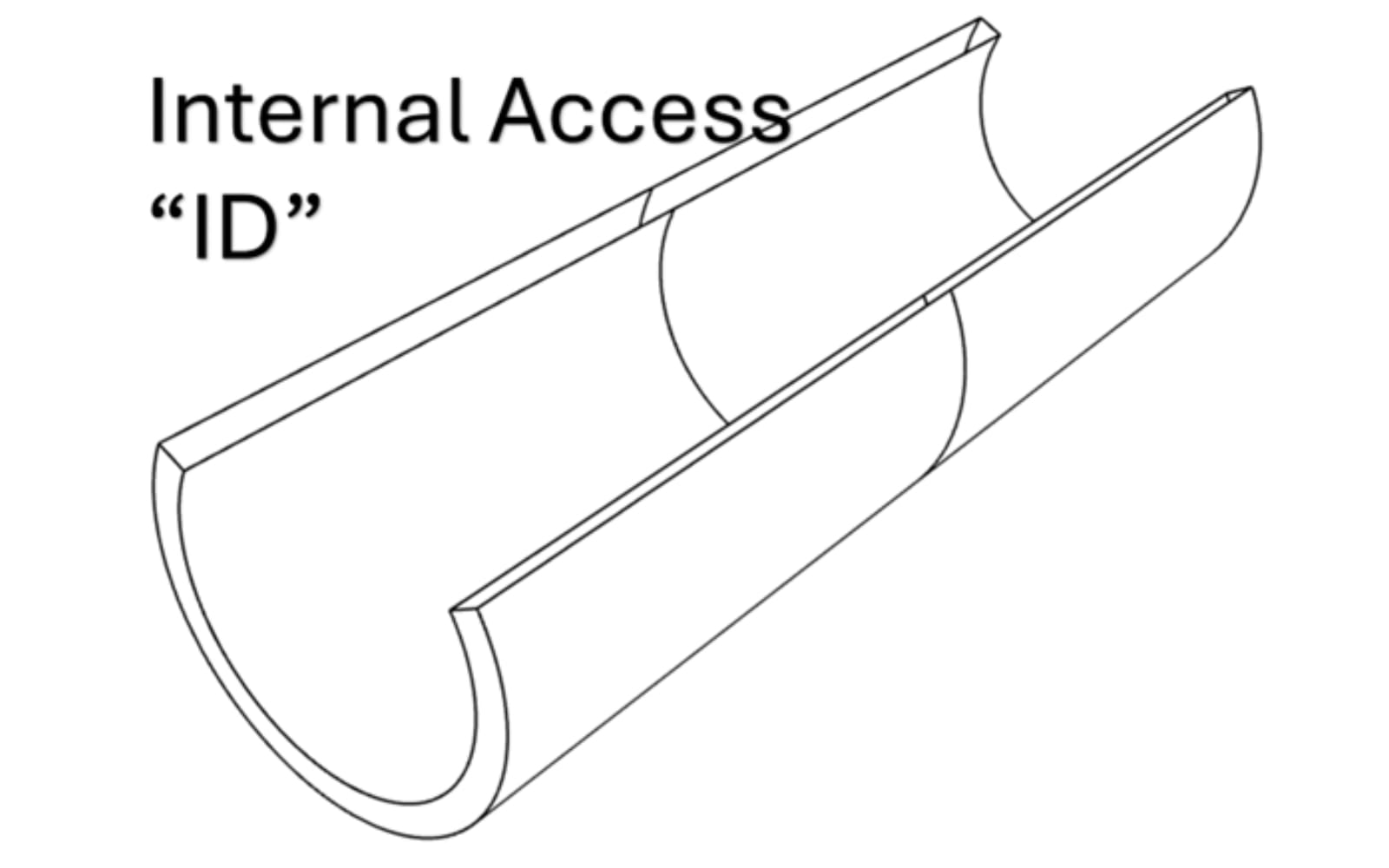
Techniques:
- Automated & Semi-Automated Phased Array Ultrasound & UT
- Visual Inspection using Remote Cameras (RVI)
- In-line Inspection with UT and MFL (Pigging)
Extra Challenges
- Height clearance
- Scanners and crawlers’ technologies investment (pigging)
- Inner surface conditions may affect crawling and NDT evaluation performance
- The overall setup requires reliable components of:
- Remote controls (visual and signal acquisition)
- Constant irrigation
- Post-analysis software
- Qualified NDT and crawler operators’ teamwork
Challenges for some locations and flaw characterisations
The previous tables contain only the typical challenges that an NDT service provider can face. Fortunately, there are many solutions to overcome most of the difficult aspects of pipeline inspections.
Here are a few examples of when the NDT advances through the pipeline industry requirements.
- Small footprint PA probe → Low clearance access, single access weld on flanges.
- Rolling probes with Glycol under cold conditions → Clear off the water coupling freezing issues.
- EMAT probe → When water coupling is now allowed.
- Pulsed Eddy current mapping → Allows a full screening mapping without preparation. (Magnetic field penetrates through the insulation)
- The use of CAD overlay → To superimpose ultrasound images or RT shots to spot any dissimilarities.
- AI & smart post-analysis software tools → Some NDT data is hard to interpret (like TOFD, Acoustic emissions or LRUT data) The software will detect and flag anomalies. Software evaluation tools are also more precise.
What’s Next?
Because we are engineering ultrasound solutions, the NDT piping solution focus will move on to PAUT, TFM, TOFD, etc. There are indeed many ultrasound techniques that gravitate around the pipeline asset. Each has pros and cons, but certainly, achieving reliable quality control that also fulfils a good practice standard.
For more information please get in touch.
Please contact our Applications Team if you have any questions. You can also find more solutions on our website.
To follow further content and our newsletter, please contact us and check “Add to mailing list”.