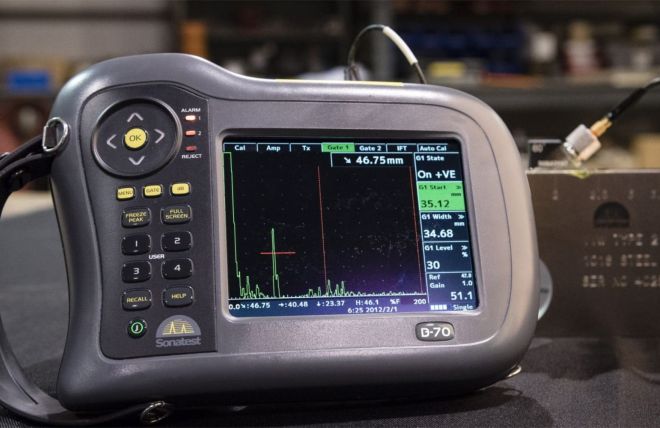
Linear scanning is an appropriate method for inspecting composite materials, but the workflow must be respected. Robust plan limits errors and confirms quality monitoring.
Among the main benefits of workflow, there are a more efficient process and a sequential order that ensures that all stages have been correctly completed. For linear array evaluation, the workflow has three simple steps:

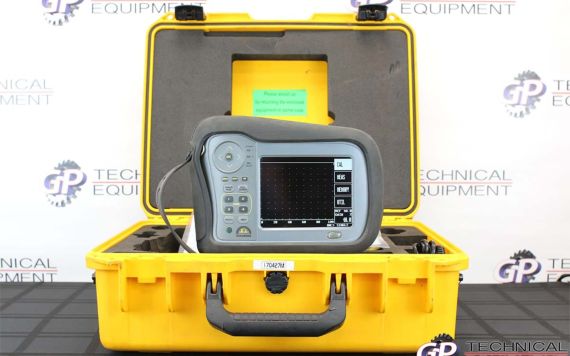
Linear Workflow Solution Package
Scan
The scan section can be summarised as the parameters to be considered for composite structure analysis probe.
An A-Scan quality data set is the basis of the acquisition. Actually, a C-Scan uses a data gate to extract information from A-scan data. Since composite inspection is suitable with straight beam linear scan, C-scan allows a excellent visualisation of discontinuities. These may be, in others, delamination, porosities, disbond, etc. Moreover, another advantageous practice is to overlap C-scans, especially with large areas, like it is the case for an aircraft fuselage. C-scan data are considered as strips. They can therefore be juxtaposed or stitched during report process.
Record
Apparatus employs must be adapted to the needs of the technician as well as the part to examine. In the composite industry, the key solution is Linear scan array inspection (L-Scan). A device that meets these criteria is straightforward to use. Indeed, the operator does not have to consider beam steering with this UT method, which facilitates calibration process. Therefore, the training for the operator is reduced. It all comes down to save time.
Report
At a glance, a report sums up the inspection made. It must be clear, concise and visual. C-scan and their functionalities are the best way to meet these requirements. Indeed, scan stripes from different sections create a meaningful image for analysis and reporting. Likewise, automatic annotation measurement tools facilitate report writing while accentuate default areas. The major benefits of this approach are dimension precision improvements and repeatability as well as fast and reliable.
With these three phases, this optimises the workflow for a fast data acquisition which is a time saver for the operator. The combination of three steps together, which can be translated as devices in fact, reduces the entire inspection process from acquisition to submission a final report.
Please contact our Applications Team if you have any questions. You can also find more solutions on our website.
To follow further content and our newsletter, please contact us and check “Add to mailing list”.