- Application Notes
Flange Inspection Live TFM
Flanges are found everywhere in industry, they are the main form of connecting pipeline lengths to other pipes, valves, vessels etc. They are often exposed to corrosive fluids and challenging environments that can cause damage over time, potentially leading to failure. Accordingly, it is vital that any degradation is identified during inspections to maintain the asset and avoid leakage or catastrophic failure.
Visual inspection is a common method for inspecting flanges but this means having to shut down the plant and open the flanges which costs time and money. Phased array allows the inspection of flanges, in service, without having to take them apart, resulting in quicker and lower cost inspections.
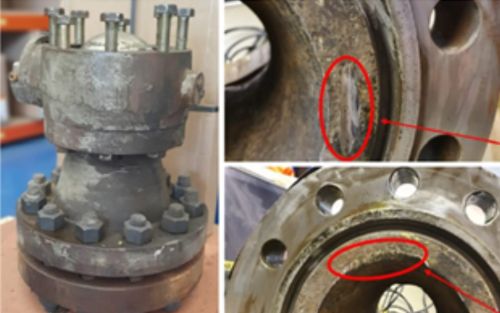
Fig. 1 - Flange face defects
Inspection information
The inspection was performed from the flange face as shown in the image below, this is usually a fully accessible surface for in situ inspections.
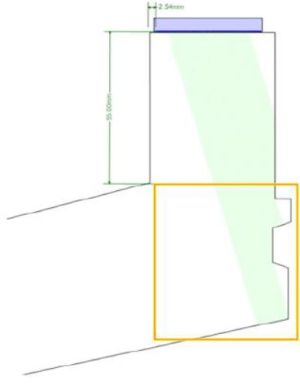
Fig. 2 - Flange inspection scan plan
- A 5MHz, 64-element PAUT transducer was used for this inspection. Smaller probes may also be used to get a greater amount of coverage
- For best results, the inspection should be encoded. Specific scanners can also be used, when applicable
- Between 50% and 70% coverage of the flange face is achievable when inspecting from the bolt face using a PA scan
- Combined with a TFM LL mode scan, the profile assessment is greatly improved. LL stands for direct mode and is based on the compression wave velocity TFM scan type
The inspected flange has a groove for the gasket (it can be seen in the image above). It can be suseptable to corrosion and pitting. The following figures show the results of an inspection on this area.
When detecting defects on the flange face, the extractor box’s position is moved so that it covers the area between the grove and inside corner of the flange. The image below shows the full top view. You can easily spot the good and bad areas.
The sample has two defects in the flange face: one central and one on the edge, as shown in the images at the beginning of this application note. Please see the images below, which show how the defects appear after an inspection.
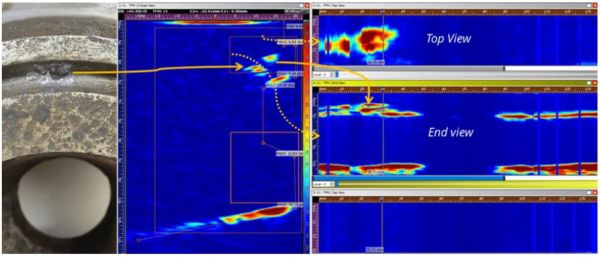
Fig. 3 - Defect detection of wall losses in the flange face groove
The flange lip geometry generates a corner echo. A new or an undamaged flange will define a back-wall echo following the internal pipe. It is shown in Figure 4. The Live TFM view and extracted view include visual hints; any echo changes will be spotted immediately.
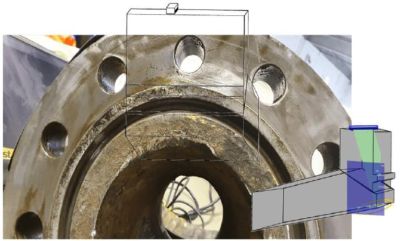
Fig. 4 - Flange edge and its TFM scan location
Specifically, on the further flat echo, it matches the inner pipe surface location. It also reaches the flange corner when it is not damaged. The corroded feature #2 (encircled in orange in Figure 2) has an angled face that deflects the sound when the flange grooves are rounded. Therefore, this inner echo should fade away as it gets further damaged.
Conclusion
- TFM, using the LL propagation mode, provides a clean “shot” of the flange’s inner face and grooves
- The interpretation of the scan is improved by using UTstudio+
- Using multiple extracted views on a specific area enhances the analysis of complex areas
- With improved CAD tools, BeamTool 9 remains the best software to create this scan plan
- It would not be possible to get 100% coverage of the flange face using this method as some areas are blocked by bolt holes.
Recommended Tool Package
Category | Part# | Description |
---|---|---|
Acquisition Unit | VEO3 phased array data acquisition unit | |
Probe | D1A 5M32E probe and D1AW N60S wedge | |
Encoder | AXYS Encoder |
Please contact our Applications Team if you have any questions. You can also find more solutions on our website.
To follow further content and our newsletter, please contact us and check “Add to mailing list”.
Filter by Industry
- Aerospace Aeronautical
- Aerospace Astronautical
- Chemical & Petrochemical
- Oil & Gas
- Nuclear Energy
- Wind Power Renewables
- Transport Network Infrastructure
- Rail
- Military
- Maritime Shipping
- Automotive
- Pharmaceutical
- Mining
- Construction & Infrastructure
- Technology & Research
- NDT Service Providers
- NDT Education
Related Products