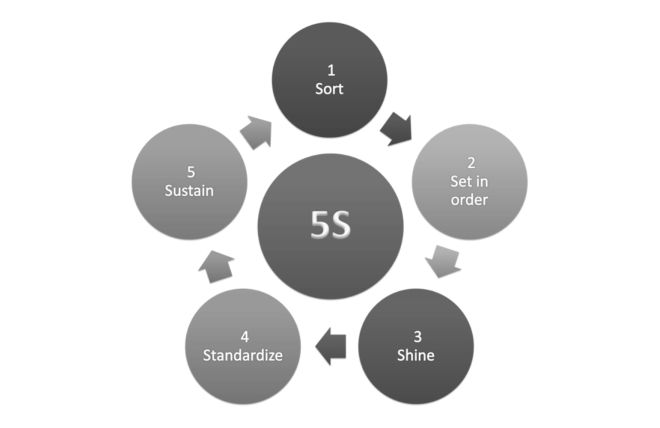
In today's dynamic industrial landscape, aerospace continuously strives for elevated quality standards. Effective quality control programs, namely driven by NADCAP or AS9100, not only ensure rigorous processes are in place but also help mitigate potential maintenance issues by incorporating a continuous improvement approach.
Ensure Procedure Compliance with a Controlled Workflow Environment
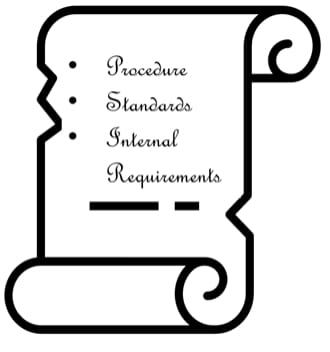
To state the obvious, aircraft manufacturers cannot underestimate the small risks associated with both maintenance and new parts for new planes.
The quality of supplier parts, minimizing maintenance expenses, and ensuring the longevity of each airplane are top safety priorities, and that is why NDT is a big part of this industry. Of course, NDT equipment, namely ultrasonic flaw detectors, plays a crucial role in enabling strict inspection procedures. Unlike regular and predictable manufacturing processes, quality control through NDT, particularly ultrasonic testing, is a large reliance on the technicians' ability. Auditing and ensuring process compliance of inspection procedures can be daunting, especially for manual inspection.
The Sonatest Wave aims to transform what is today seen as a burden into a lever for greater efficiency and effortless compliance.
The Inspector and Their Instruments
A significant portion of the challenge and responsibility rests on the inspectors’ shoulders. They must accomplish their duties while striving to minimize errors throughout the day.
At Sonatest, our Wave instrument aligns with the 5S system in a uniquely integrated manner.
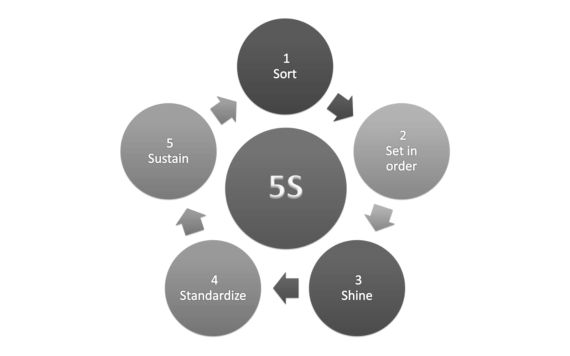
The PC Wave Companion software takes complete control of the interface for each flaw detector, allowing users to effortlessly execute a series of Wapp Apps (Interface customisations and default parameters) that expertly guide various ultrasound tasks.
5 Key Points Working Together
- You can sort all the interface items to prioritise or eliminate unnecessary parameters. This way, only the necessary controls are available, and you ensure that the settings are the correct ones.
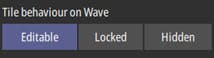
- You can set menus and tiles in a logical order so that the objects work from left to right. Essentially, you fit the user interface with the workflow, not the other way around
- Global Parts to Calibration menus to Assessment Measurements
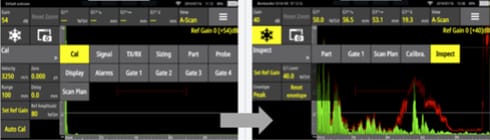
- Each Wave app shines (the interface appears insightful and targets a clear inspection) and has its distinctive recipe, and everything is streamlined and clean. You can also personalise it with a meaningful description.
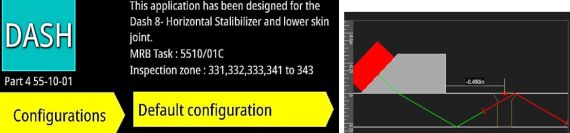
- You can import relevant PDFs for each app so the tasks and procedures are available during the inspection, a practice that contributes to standardising your system.
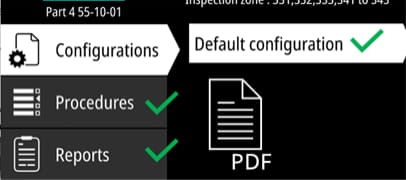
- By replicating this process for new inspections, you establish a sustainable environment for the inspector.
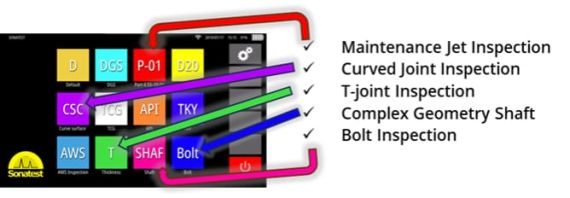
The Wave App becomes the Procedure
The following example can be used for other purposes, the idea is to reproduce the procedure plan.
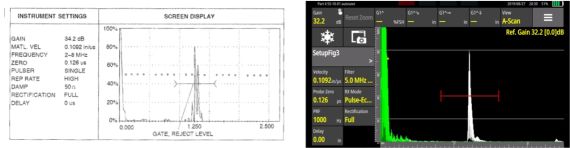
The Wave software can replicate all the NDT activity requirements as described in its paperwork. The figure above depicts an inspection scenario for a DASH 8 horizontal stabilizer and lower skin joint (MRB task 5510/01C). The aerospace industry adheres to many stringent procedures, each unique in its own. With a simple click, the app initiates and loads all the recipe content, encompassing the required parameters and procedures.
App Benefits
In this manner, any Wave App you create becomes a controlled and auditable digital workflow for an existing inspection procedure. Consequently, subsequent users tasked with the same inspection can simply activate the app, avoiding the need to configure parameters anew. This level of control ensures that even interns or entry-level UT personnel can execute inspections confidently, without altering critical parameters.
Of course, adherence to conformity involves more than just device features; it combines training certifications, self-awareness, experience, etc.
When we developed our software environment, we thought of all possible nonconformities so the Wave mitigates the user's potential errors.
In conclusion, our instrument enhances the quality of inspections, benefiting inspectors and equally assuring managers who prioritize a secure approach through the use of Wave and its seamless integration for high-level inspection procedures.
Please contact our Applications Team if you have any questions. You can also find more solutions on our website.
To follow further content and our newsletter, please contact us and check “Add to mailing list”.
Related Products