Ultrasonic Flaw Detection
Ultrasonic Testing (UT), a method of Non-destructive Testing (NDT), is a widely used technique for inspecting metallic, plastic and composite materials, allowing for the detection of wall loss and imperfections in the material body and surfaces.
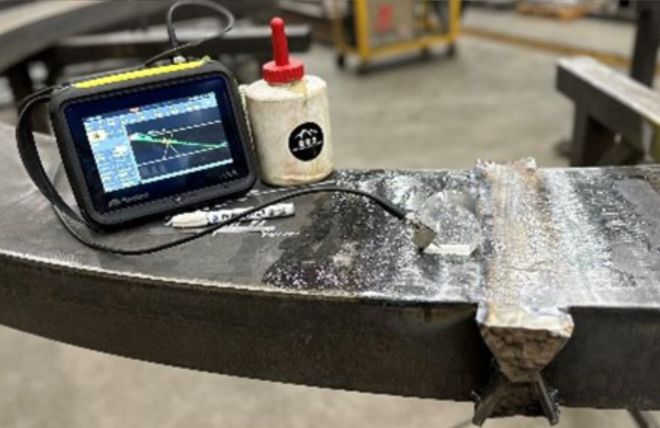
Basic Principles
UT inspection is based on the propagation of soundwaves in a material. We can produce an ultrasonic pulse in a material and time how long that signal takes to ‘echo’ off the back wall and return to the surface. Using the speed of ultrasound, we can calculate the wall thickness of the material and identify any wall losses or internal discontinuities present in the material.
All ultrasonic techniques work on this basic principle with increasing levels of complexity and equipment computing power. From UT thickness surveys to weld and Phased Array inspections to full matrix capture and Time of Flight Diffraction techniques, all can be traced back to the principle of timing sound travelling through a material.
Equipment
To produce an ultrasonic pulse within a material and to display and calculate results, we require a ‘transducer’ or ‘probe’ to transmit and receive the ultrasonic signal, and a control unit that produces the pulse within the transducer carries out all the measurements calculations and displays the results in an A-Scan.
At Sonatest, we manufacture all the equipment required for these inspections. Follow the links to see our range of Ultrasonic Flaw Detectors, Transducers, and our library of application notes, solution notes and educational material.
Applications
Ultrasonic inspection has many applications across multiple industries. A few examples are given below.
Corrosion assessments - 0° inspections are widely used in industry to detect and provide information on corrosion in pipelines, storage vessels and structures. This can include the remaining wall thickness and the overall size of the corroded areas.
Weld Inspections - 0° and angled ultrasonic inspections are used to evaluate weldments and detect manufacturing defects as well as in-service defects.
Composite structure assessments – Conventional UT pulse echo and thorough transmission methods are used to evaluate composite structures for laminations, porosity and bonding issues.
Please contact our Applications Team if you have any questions. You can also find more solutions on our website.
To follow further content and our newsletter, please contact us and check “Add to mailing list”.