WAVE
The WAVE interactive flaw detector integrates the latest technologies available in order to create a revolution in the ultrasonic non-destructive testing equipment market.
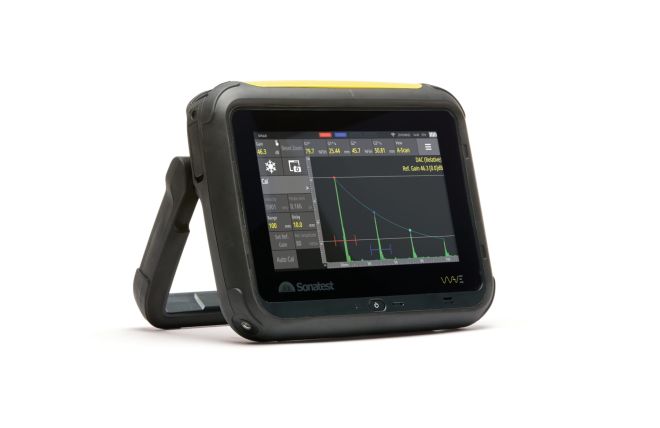
Overview
Next generation technology at your fingertips
What if you could tailor the settings on your UT device and alter it to your own process and people’s needs? An instrument where all the useful parameters are pre-set and available in less than two clicks? Now you can.
Introducing WAVE by Sonatest. It integrates the latest technologies available in order to create a revolution in the ultrasonic non-destructive testing equipment market. Not only is it innovative, but the customisable interface also optimises the daily workflow, and a unique and embedded interactive scan plan, with ray-tracing capability, simulation tools and CAD import capability, consolidates your results.
Its wifi capability allows you to access it anywhere in the field, eases data transfer, application installation and manages calibration date and software version.
Features
Interactive Scan Plan
Mitigate false calls with the new WAVE Interactive Scan Plan
The WAVE Interactive Scan Plan has been developed to ease diagnostics on the inspected part. The scan plan can reproduce complex geometries such as curved surfaces and T-Joints. Combined with a real-time Raytracer, this unique feature facilitates the distinction between a real flaw and a geometrical indication, thus avoiding unnecessary repair.
Import Custom Parts
The WAVE can import a custom part in the interactive scan plan. This feature enables the user to visualise sound propagation in complex geometries. All the benefit of the Interactive Scan Plan remains with the addition of removing the limitations that come with predefine parts.
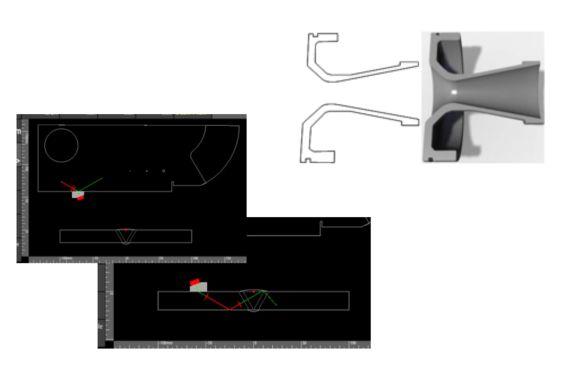
UTouch Technology
UTouch Technology allows your device to operate in the same way as a mobile phone. Combined with rugged components and an intelligent algorithm which makes the distinction between couplant and finger.
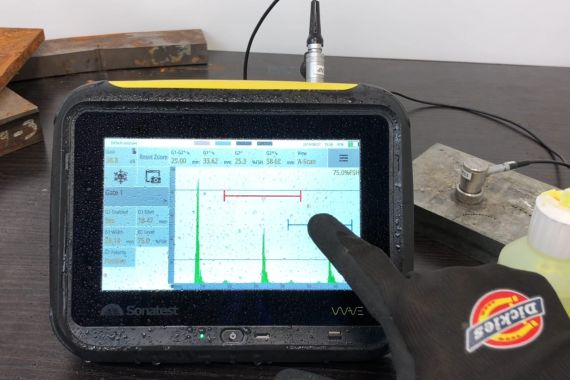
Application Concept
The WAVE appliction concept combines conformity and performance which allows the operator to customise the user interface according to their specific procedure.
The intuitive user interface with an easy to use display will guarantee workflow optimisationas well as preventing potential operational errors.
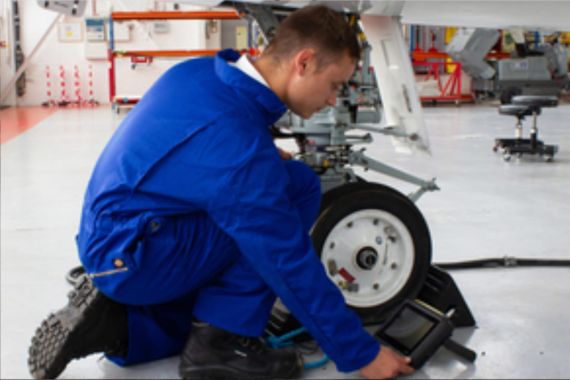
WAVE Companion Software
The WAVE Companion software offers an evironment where dedicated predefined applications setups are created and uploaded to WAVE platform.
Once created, the new app setups are transferred and installed on the unit via wired (USB-C / ethernet) or wireless network. The default app allows access to all functionalities and features where the user can modify the entire settings.
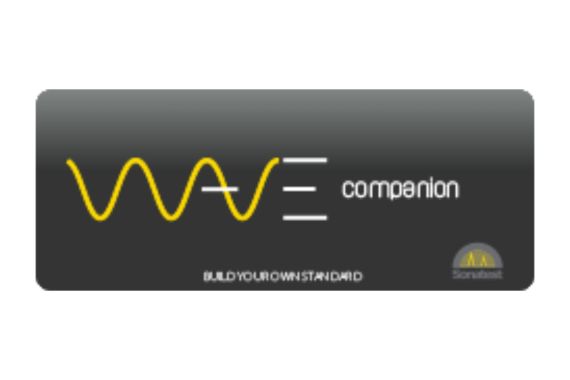
Ask an Expert Download Brochure (460.9KB) Request a Demo
Specification
WAVE Concept | |
Wave Applications | Up to 50 Apps |
Wave UTouch Technology | P-CAP Multi Touch |
Remote Application Protocol Interface | MQTT 5 Specification |
Interactive Scan plan | |
Crown and Root Geometries | Yes |
Weld Overlay | Yes |
TKY/ Nozzle/ Flange Geometries | Yes |
Curved Surface | Yes |
Live Raytracer | Yes |
Projected A-Scan | Yes |
True Depth on Complex Shapes | Yes |
Custom CAD Import | Yes |
Measurements | |
Gates | 4 |
IFT | Yes |
DAC/Split DAC | Standard |
TCG | Standard |
AVG/DGS | Standard |
AWS | Standard |
API | Standard |
BEA | Standard |
Curved Surface Correction (CSC) | Standard |
TKY and Complex Shapes | Standard |
Transmitter | |
PRF | 1500Hz |
Pulser (Voltage) | 100 to 500V |
Receiver | |
Gain Range | 110dB |
Bandwidth | 0.25 to 30MHz |
Filters | 26 filters |
Signal Averaging | Yes |
General | |
Battery Life | 10 Hours |
Display Size (Resolution) | 7" wide (1024 x 600) |
Dimensions mm (in) | 222 x 174 x 63 (8.7 x 6.8 x 2.5) |
Weight kg (lb) | 1.7 (3.7) |
IP Rating | Designed for IP 67 |
Operation Temperature | -10°C to 45°C |
Wifi (embedded) | Yes |
Ask an Expert Download Brochure (460.9KB) Request a Demo
Accessories
WAVE: Lemo
Product Number | Description |
---|---|
WAVE Lemo unit | |
195000 | WAVE Carry Case |
242000 | WAVE Smart Li-ion Battery Pack |
800001 | WAVE AC/DC Battery Charger |
WAVE-ACC-001 | WAVE Hand Strap Assembly |
136001 | Ethernet to USB Adaptor |
192001 | Ethernet Cable 1m |
147441 | Quick Start Guide |
WAVE-ACC-004 | Screen Protector Kit (CLEAR) |
WAVE-ACC-005 | Screen Protector (TINT) |
WAVE: BNC
Product Number | Description |
---|---|
WAVE BNC unit | |
195000 | WAVE Carry Case |
242000 | WAVE Smart Li-ion Battery Pack |
800001 | WAVE AC/DC Battery Charger |
WAVE-ACC-001 | WAVE Hand Strap Assembly |
136001 | Ethernet to USB Adaptor |
192001 | Ethernet Cable 1m |
147441 | Quick Start Guide |
WAVE-ACC-004 | Screen Protector Kit (CLEAR) |
WAVE-ACC-005 | Screen Protector (TINT) |
Accessories & Spares
Product Number | Description |
---|---|
WAVE-ACC-001 | Wave Hand Strap |
WAVE-ACC-002 | 4-Point Working Harness |
WAVE-ACC-003 | Single Point Safety Harness |
WAVE-ACC-004 | Screen Protector Kit (CLEAR) |
WAVE-ACC-005 | Screen Protector Kit (TINT) |
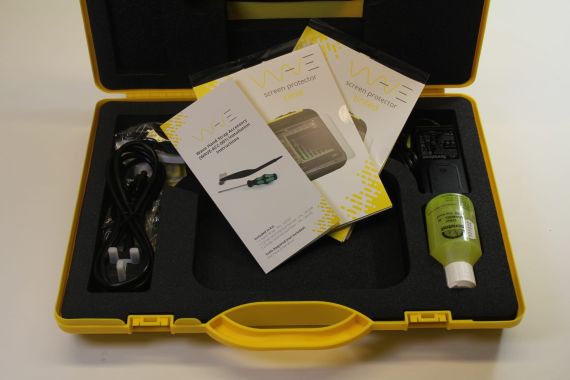
Ask an Expert Download Brochure (460.9KB) Request a Demo
Downloads
Brochure & Specification
Type | Title | Size | |
---|---|---|---|
Wave Brochure (July 2024) | Download | 0.45 MB | |
Wave Full Specification | Download | 0.09 MB |
Li-Ion Battery Information
Type | Title | Size | |
---|---|---|---|
LG Li-ion Battery Pack Declaration of Conformance | Download | 0.77 MB | |
LG Li-ion Battery Pack Information Sheet | Download | 0.66 MB | |
LG Li-ion Battery Packs Test Summary | Download | 0.16 MB |
Software
Ask an Expert Download Brochure (460.9KB) Request a Demo