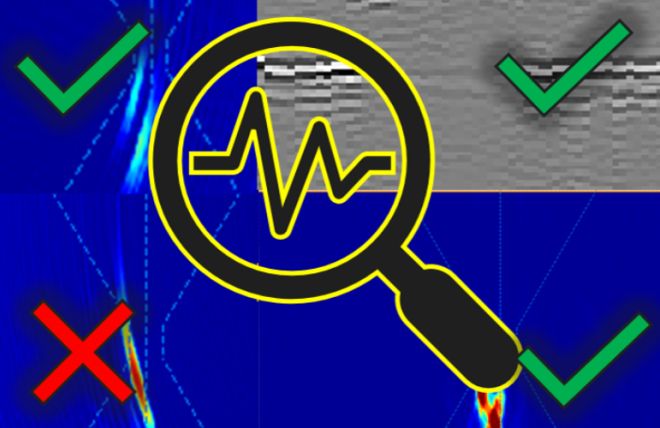
The recent development of the Total Focusing Method (TFM) in non-destructive testing has been recently outlined in eight studies in the past 3 years, each progressively refining flaw detection and sizing methodologies.
Reliability assessment of different NDT methods - 2023[1]
Since non-destructive testing (NDT) methods are used to detect and characterize flaws, this study aimed to evaluate the reliability of NDT methods for inspecting weld joints in hydraulic turbine runners. Conventional ultrasonic testing (UT), radiographic testing (RT), phased array ultrasonic testing (PAUT), and the total focusing method (TFM) were compared. The NDT tests were conducted on a T-joint specimen manufactured with embedded flaws. This specimen was used to determine the probability of detection (POD) curves for volumetric flaw sizes. The results showed that TFM demonstrated a detection capability (a90) around 2.5 mm, which is similar to the commonly used equivalent critical flaw size for such structures. It was observed that TFM produced a detailed image of an indication’s reflective surface and effectively characterised and sized indications.
TFM applied to POD – 2023[2]
In this paper, TFM was used as a tool to provide accurate flaw sizing for POD determinations. This study was one of the first to propose TFM as the basis for flaw sizing in POD evaluations. It presented the motivation and a new methodology for generating POD curves, largely based on TFM examinations, to obtain reference flaw size information. The results showed the feasibility of developing POD curves without destructive analysis, using TFM to acquire flaw size data.
Fitness for service (F.F.S) assessment – 2023[3]
In this study on assessing flaws for the fitness-for-service (F.F.S) evaluation of turbine runners, sizing assessments of side-drilled holes (SDH) were carried out using TFM. Depending on the probe used, mean sizing errors of 0.88 mm were obtained for probes focused in the passive axis and 0.55 mm for unfocused probes. Additionally, the performance of both PAUT and TFM was evaluated for inspecting critical areas in the welded joints, with specific emphasis on using TFM for flaw sizing (length, height, and ligament of flaws). The results indicated that TFM-based flaw sizing is more accurate than to other ultrasonic testing techniques for the F.F.S assessment of hydraulic turbine runners.
Simulation of Defects to Gather a Complete POD Study – 2022[4]
Building on these advancements, the study, “Total Focusing Method Used for Flaw Sizing in Probability of Detection Determination,” explored TFM’s role in creating Probability of Detection (POD) curves. This paper examined flaw sizing and ligament measurements, emphasising the importance of accurate dimensioning for assessing POD. By addressing variability in sizing tolerances and incorporating flaw-specific analyses, this research validated TFM’s potential to provide consistent and reliable results under diverse defect scenarios. The paper concludes that TFM alone can be used to establish an accurate flaw-size evaluation for POD.
Simulated Defects Being Analysed by Random Inspectors – 2023[5]
The paper, “Stage 1 Round-Robin Report: On the Use of Total Focusing Method for Sizing Flaws,” provided a broader analysis through a collaborative trial using simulated weld scenarios. The study emphasised practical challenges in adopting TFM, such as algorithm variability and operator experience, while recommending pathways for improvement. It underscored that operator expertise and workflow standardisation are critical in achieving reliable and repeatable TFM outcomes.
TFM Performance on EDM Notches – 2024[6]
The paper, “Developing Flaw Sizing Methodology in Total Focusing Method (TFM) by EDM Calibration Blocks,” laid the groundwork for more accurate TFM applications. It introduced electrical discharge machined (EDM) calibration blocks, which better represented real-world flaws compared to traditional side-drilled holes (SDHs). These EDM notches simulated complex geometries, significantly improving TFM’s precision in capturing flaw characteristics and establishing a more reliable basis for flaw sizing in practical applications. The very last sentence revealed the importance of implementing a solid post-analysis process based on each unique context of NDT inspection: - “This study highlights the importance of adopting a tailored approach to flaw sizing, considering the unique context and requirements of each inspection scenario.”
Artificial Defects with Known Location; Evaluating Human Analysis Performance – 2024[7]
The study, “Evaluating Human Factors in TFM Sizing Accuracy: Statistical Findings from a Round-Robin Programme (Part 2),” is the first to introduce human-related influences on TFM results. It highlighted the variability introduced by individual expertise, decision-making, and interpretation. The statistical evaluation revealed that differences in training significantly impact flaw sizing accuracy, suggesting that consistent training and streamlined workflows could mitigate human factors. The user determined the region of interest resolution, which could have an impact on the analysis results.
Blind Test on Artificial Defects by Inspector Contestants [8]
The Sonatest research study was made to compare the TFM/TFMi performance against the Sectorial Scans (S-scans) and Time of Flight Diffraction (TOFD). Weld samples with known defects, such as cracks, porosity, and slag inclusions, were analysed independently by experts, ensuring unbiased results with minimal human influence. While TFMi™ demonstrated promising results in reducing error rates and improving flaw characterisation, the study underscores the importance of refining imaging tools and post-analysis methods across all techniques.
Height Precision Wrap-up
The theory begins with simulated data files. The theory behind diffraction tip measurement associated with the probe wavelength is under the 1.0 mm length. When you combine all the little errors around the acquisitions, the post-analysis tooling, and human factors, the height error increases relatively but remains just above the 1.0 mm level.
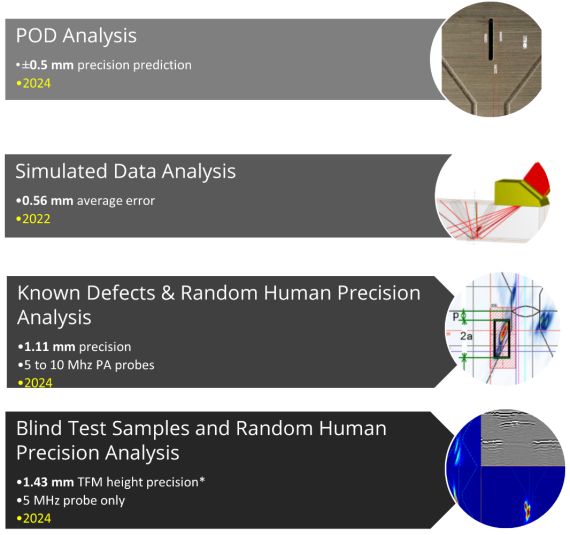
*The other techniques have obtained a height precision of 1.77 mm at TOFD, 1.55 mm at PA S-scan and 1.55 at TFMi.
Conclusion
Together, these studies illustrate the progressive development of TFM, from improved calibration methodologies to addressing POD requirements, workflow standardisation, and human-related challenges.
There is an interesting common statement among the studies, and it underlines the importance of a detailed post analysis evaluation, when it comes to assessing the flaw size. With the last study that Sonatest did with TFM, we commit to share the best practices according to the gathered data based on the inspector mistakes.
Please contact our Applications Team if you have any questions. You can also find more solutions on our website.
To follow further content and our newsletter, please contact us and check “Add to mailing list”.
[1] M.E. Bajgholi, G. Rousseau, M. Viens, D. Thibault, M. Gagnon, Reliability assessment of non-destructive testing (NDT) for the inspection of weld joints in the hydroelectric turbine industry, The International Journal of Advanced Manufacturing Technology, Springer Publisher, Vol. 128, No. 9, 2023, pp. 4223–4233.
[2] M.E. Bajgholi, G. Rousseau, E. Ginzel, D. Thibault, M. Viens, Total focusing method applied to probability of detection, The International Journal of Advanced Manufacturing Technology, Springer Publisher, Vol. 126, No. 8, 2023, pp. 3637–3647.
[3] M.E. Bajgholi, G. Rousseau, M. Viens, D. Thibault, Advanced ultrasonic inspection methodologies for fitness-for-service (FFS) assessment of hydraulic turbines, The International Journal of Advanced Manufacturing Technology, Springer Publisher, Vol. 129, No. 5, 2023, pp. 2621–2633. DOI: 10.1007/s00170-023-12498-4.
[4] E. Ginzel, M.E. Bajgholi , M. Burrowes, M. Guimarães, F. Foucher, Gilles Rousseau, Martin Viens, Total Focusing Method used for flaw sizing in probability of detection determination. NDT.net. June 2022. https://www.ndt.net/article/ndtnet/papers/TFM_used_for_flaw_sizing_for_probability_of_detection_determination.pdf
[5] Burrowes, M., Ginzel, E., Pereira, G.R., Tavares, L.M., Stage 1 Round-Robin Report: On the Use of Total Focusing Method for Sizing Flaws in Assessing Probability of Detection, NDT.net August 2023, https://www.ndt.net/article/ndtnet/papers/Stage_1_Round-Robin_Report_On_the_Use_of_Total_Focusing_Method_for_Sizing_Flaws_in_Assessing_Probability_of_Detection.pdf
[6] M.E. Bajgholi, G. Rousseau, E. Ginzel, M. Viens , V. Mélançon, Developing flaw sizing methodology in Total Focusing Method (TFM) by EDM calibration blocks, Vol. 29(10), 2024. https://www.ndt.net/article/ndtnet/papers/Developing_flaw_sizing_methodology_in_Total_Focusing_Method.pdf
[7] M. Burrowes, E. Ginzel, G. R. Pereira, C. G. Camerini. Evaluating Human Factors in TFM Sizing Accuracy: Statistical Findings from a Round-Robin Programme (Part 2). December 2024. https://www.ndt.net/article/ndtnet/papers/Evaluating_Human_Factors_in_TFM_Sizing_Accuracy_Statistical_Findings_from_a_Round-Robin_Programme_2.pdf
[8] P. Rioux, W. Haworth, S. Hughes. Intermodal Total Focusing Method (TFMiTM) and Multi-technique Ultrasonic Sizing Analysis Study. Sonatest AP; Québec, Canada. https://sonatest.com/application/files/5716/9537/8242/Intermodal_TFM_with_Applications_to_Weld_Inspections.pdf